Understanding IIoT’s Role in Manufacturing Efficiency in Thailand
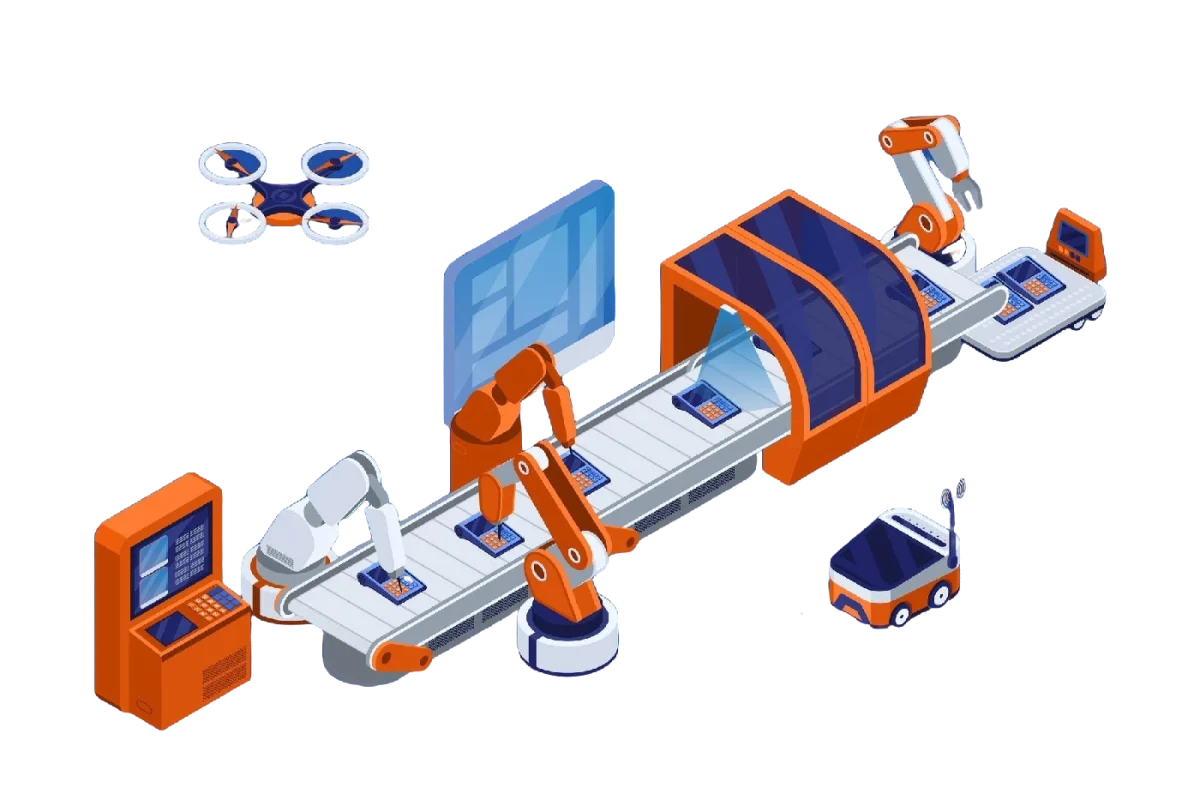
In recent years, the Industrial Internet of Things (IIoT) has reshaped global manufacturing. For Thailand, known for its robust manufacturing sector across industries like automotive, electronics, and food processing, IIoT technologies are proving transformative. IIoT is central to Industry 4.0, characterized by connected devices, automation, and data-driven decision-making. For Thai manufacturers aiming to stay competitive, understanding and integrating IIoT is essential.
Key Concepts: Industry 4.0, IoT, and IIoT
Industry 4.0 represents the latest revolution in industrial technology. In Thailand, where Industry 2.0 (electric power) and Industry 3.0 (digital computing) still drive many factories, the transition to Industry 4.0 and IIoT can be revolutionary. IIoT—an extension of the Internet of Things (IoT) specific to industrial applications—connects factory machinery, sensors, and devices to the internet, enabling “smart” manufacturing facilities. For Thailand, this means moving beyond traditional, labor-intensive practices to more efficient, interconnected systems, where data flows seamlessly between machines and across production lines.
Enhancing Efficiency Through Visibility and Remote Access
Visibility in manufacturing allows plant operators to monitor machinery in real-time and access historical data, crucial for minimizing downtime and maximizing output. Traditional methods rely on physical indicators, like tower lights, which alert operators to machine issues only if they are within sight. IIoT enhances this by connecting these lights to wireless networks, allowing operators in Thai factories to receive immediate alerts, regardless of their location.
For example, consider a Thai electronics manufacturer using IIoT-enabled tower lights and sensors. These devices log data on machine uptime, production output, and even rejected parts, creating a comprehensive performance history. Such visibility not only helps operators respond to real-time alerts but also empowers them with data to make strategic improvements in production processes.
Predictive Maintenance: Proactive Care for Maximum Uptime
In traditional Thai manufacturing, machinery is often serviced on a fixed schedule, following manufacturer recommendations rather than real-time performance data. This can lead to either unnecessary maintenance or, worse, unplanned breakdowns. IIoT shifts this approach to predictive maintenance, where sensors measure factors like temperature and vibration to detect early signs of wear. This predictive capability allows factories to replace parts only when needed, optimizing costs and avoiding unnecessary downtime.
Take Thailand’s automotive sector as an example, where high productivity is essential to meet export demands. By implementing IIoT predictive maintenance, automotive factories can detect and resolve issues before they escalate, ensuring a continuous production flow.
Streamlined Communication Across the Factory Floor
IIoT also improves communication between machines and human operators. Instead of operators walking across factory floors to request assistance, IIoT-enabled push buttons and tower lights can signal a need for help instantly. In Thailand, where manufacturing sites are often large and rely heavily on manual processes, this real-time communication streamlines operations.
Consider a food processing factory in Thailand where assembly line workers signal for assistance by pressing a button. The IIoT system immediately alerts the appropriate supervisor or technician, reducing wait times and keeping the line moving. This interconnected setup not only increases productivity but also enhances worker efficiency, a critical factor in Thailand’s competitive manufacturing landscape.
Is Your Business in Thailand Ready for IIoT?
For Thai manufacturers, adopting IIoT is about more than technology—it’s about cultural and operational shifts. Thai manufacturers must first assess their operational inefficiencies and the type of data that could address these issues. Additionally, they need to build communication processes that can leverage IIoT insights. Starting with these foundational steps, Thailand’s manufacturing sector can tap into the powerful benefits of IIoT to drive efficiency, lower costs, and remain competitive in a global market.
Embracing IIoT is not just an investment in technology but an investment in the future of Thai manufacturing, promising a more efficient, data-driven approach to production and innovation.